How To: Handle Micro Fasteners
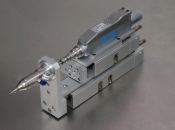
Weber Screwdriving Systems Inc. has incorporated micro piezoelectric technology into its micro feeding solutions. The science behind piezo technology incorporates piezoelectric crystals that vibrate at different frequencies depending on the voltage & current being passed through them, rather than using electromagnetic coils. Weber USA undertook the development of a new version of the piezo feeder which would move fasteners using micro-vibrations which are gentler on the small fasteners. This allowed the Micro Piezo feeder to successfully feed micro fasteners, pins, and other small shapes very quickly without any issues.
Driving and installation of micro fasteners requires a Micro screwdriving spindle with special features such as integrated vacuum due to their short length as the use of blow feeding delivery is, in many cases, not possible. So a pick & place vacuum spindle with extremely tight tolerances, special materials, and a low mass bit were developed which is capable of installing these fasteners with precision & repeatability. One of the major challenges in designing this spindle was the reduction of mass which resulted in low inertia to allow us to achieve the tight target torques desired without the issue of overshooting our torque target. Weight must also be reduced on all moving components when final torque is well below 1Nm. Overshooting the target isn’t the only problem plaguing micro fasteners. Often times the drag or resistance inside the spindle its self actually can cause incorrect torque readings by having drag values on the transducer. The friction in the spindle will actually reduce the final screw seating torque by the same value the friction produces. Typically this would not be an issue in larger screwdriving applications, but when torque and scale are reduced to the micro level, these factors are magnified. Weber Screwdriving Systems Inc. has managed to find a solution for all of these difficult screwdriving challenges when producing our Micro Screwdriving devices.